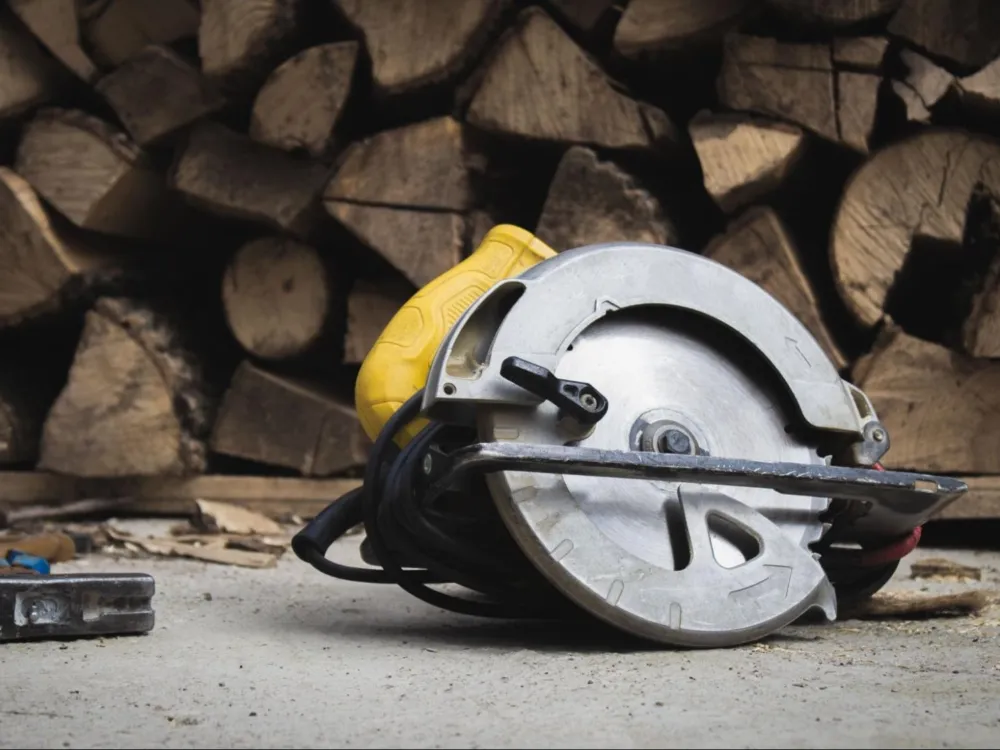
Choosing the best circular saw blade can be challenging with so many options available. This guide simplifies the process by providing detailed insights into blade types, uses, and how to select the best one for your needs. Whether you're a professional craftsman that needs a durable and precise blade for commercial projects or a hobbyist seeking versatility and ease of use, this comprehensive guide has got you covered.
The Importance of Choosing the Right Saw Blade for Optimal Cutting Performance
Selecting the right saw blade is a critical decision in woodworking, metalworking, and other construction or DIY projects.
The right blade ensures not only precision and efficiency in your cuts but also contributes to the longevity of both the blade and your saw.
Different materials and cutting tasks require specific blade types, each designed to optimize performance under certain conditions.
For instance, a blade meant for wood will differ significantly from one intended for metal or tile in terms of tooth design, size, and material.
Using the wrong blade can lead to poor cut quality, increased wear on the tool, and even pose safety risks.
The correct blade choice can save time and resources by reducing the need for additional finishing or repairs due to uneven or inaccurate cuts.
Key Factors to Consider When Selecting a Saw Blade
Choosing the right saw blade is a multifaceted decision that hinges on several key factors
- The type of projects you undertake
- The materials you frequently work with
- The dimensions of the items you're cutting
Understanding these factors ensures not only the quality and precision of your cuts, it also contributes to the safety and longevity of your sawing equipment.
Project-Specific Blade Selection
Different projects demand different blades. For instance, a blade that excels in fine woodworking may not be suitable for rough cutting or metalworking. The intricacies of the project determine the type of blade you need.
- Fine woodworking projects, like cabinetry or furniture making, require blades with more teeth for a smoother finish.
- Rough cutting tasks, such as cutting lumber for framing, need blades with fewer teeth that can remove material quickly.
Understanding the project's requirements is crucial for choosing a blade that does the job well.
Material Compatibility and Blade Types
The material you are cutting is a crucial factor in blade selection. Different materials require blades designed with specific characteristics.
- Cutting through hardwood necessitates a blade with stronger teeth and possibly a different tooth design compared to a blade used for softwood.
- Metalworking requires blades made from tougher materials like carbide, which can withstand the rigors of cutting through metal.
Using the wrong type of blade on a material can lead to inefficient cutting, and damage to both the blade and the material, and can even pose safety hazards.
Considering Object Size and Blade Length
The size and length of the objects you're cutting significantly influence your blade choice.
- Longer blades are generally needed for larger materials to ensure even and efficient cutting.
- The thickness of the blade and the number of teeth also play a role in how it handles different sizes of materials. For instance, cutting a thick piece of timber may require a blade with fewer but larger teeth to efficiently remove material and prevent clogging.
- Intricate or smaller pieces might need a blade with more teeth for finer, more precise cuts.
Making sure that the blade's dimensions are compatible with the size of the material enhances both the safety and the quality of the cut.
Blade Selection Essentials
Blade Material and Type
Blades for Wood
Standard wood blades have different tooth designs, such as rip, crosscut, and combination, each suited for specific wood-cutting needs.
- Rip blades have fewer, larger teeth for fast cuts along the grain.
- Crosscut blades have smaller teeth for smooth cuts across the grain.
- Combination blades provide a balanced option for both types of cuts.
The blade material, usually steel or carbide-tipped, should be chosen based on wood hardness and desired longevity.
Blades for General Metal Materials
Metal cutting requires blades with specific teeth counts and designs to handle the material's hardness and density.
Blades for metal often have carbide or bi-metal construction for durability.
Tooth count varies based on metal thickness; thinner metals need a higher tooth count for smoother cuts, while thicker metals require fewer, larger teeth to reduce clogging and heat buildup.
Some metal cutting blades minimize burr formation and heat generation with special tooth geometry.
Blades for Corrugated Metal
Blades for cutting corrugated metal are different from regular metal cutting blades, for several reasons:
Material Properties
Corrugated metal, often used in roofing and siding, has a unique profile with peaks and valleys. This material requires a blade that can navigate the contours without causing distortion or excessive wear.
Tooth Design
Blades for cutting corrugated metal typically have a tooth design that is more suited for the thin, wavy nature of the material. The teeth are often smaller and more closely spaced than those on standard metal cutting blades. This design helps to reduce vibration and chattering during cutting, and provides a smoother and cleaner cut.
Blade Material and Coating
These blades are usually made of high-speed steel (HSS) or have carbide tips for enhanced durability. Some may also feature special coatings or treatments that reduce friction and heat buildup, which is crucial when cutting metal in order to prevent warping or damage to the material.
Type of Saw
The choice of saw is also essential. A circular saw or a nibbler is often preferred for corrugated metal, with specific blade types designed for use with these tools. These saws allow for more precise cuts along the corrugated profile.
Application Specificity
Regular metal cutting blades are designed for a broader range of applications and metal types. In contrast, blades for corrugated metal are more specialized, and cater specifically to the challenges posed by the corrugated material.
Blades for Masonry Products
To cut masonry materials like concrete, brick, or tile, you need blades that can handle abrasion.
- Diamond blades are the most effective for masonry, with a metal blade featuring a diamond grit edge. These blades grind through the material with durability and precision.
- Another option is abrasive blades, which are cheaper, but they wear down faster. They are suitable for occasional or less demanding masonry work.
- The choice between segmented, continuous rim, or turbo rim diamond blades depends on the specific application and desired cut finish.
Choose the Proper Size
Handheld circular saws typically can accommodate 7 1/4-inch blades. On the other hand, miter or table saws are better suited for larger blades, and can reach up to 12 inches.
Teeth Count and Cut Quality
When it comes to choosing the right saw blade for your woodworking projects, the number of teeth plays a crucial role. Fewer teeth, usually between 18-30, are ideal for faster cuts, which makes them perfect for rip cuts in wood.
On the other hand, blades with more teeth, ranging from 60-80, offer smoother cuts, which makes them ideal for crosscuts. For those seeking versatility, combination blades with around 40 teeth are a great choice as they can handle different woodcuts.
If you're working with metal, there are metal cutting blades available with varying teeth counts based on the specific type of metal you're dealing with.
Tooth Angle and Cutting Method
Positive-angle teeth are designed for aggressive cuts, which makes them perfect for rough rip cuts. On the other hand, less aggressive angles are ideal for clean crosscuts. The different tooth designs cater to specific cutting needs to help ensure optimal performance for various applications.
Kerf: The Cut Width
The term "kerf" refers to the width of the cut made by the saw blade. The thicker the blade, the wider the kerf, which calls for more material removal and potentially a slower cutting speed.
Blade Requirements for Commercial vs. Hobby Use
Blades for commercial and hobby use differ significantly in their requirements due to the varying demands of each application. Understanding these differences is crucial for selecting the right blade for your needs.
Commercial Use
Durability and Longevity
In commercial settings, blades are used more frequently and intensely, so they need robust construction, often with high-grade materials like carbide or diamond tips. The goal is to minimize downtime and replacement costs.
Precision
For professional projects, precision is paramount. Commercial blades typically have a more refined tooth design and balance to help ensure accurate and clean cuts, which is crucial in a professional context.
Versatility
Blades used in commercial applications often need to handle a variety of materials and cutting conditions. This requires a design that balances flexibility with performance.
Safety Features
Given the high usage and demanding conditions, commercial blades often incorporate advanced safety features to reduce the risk of accidents.
Advantages
Increased efficiency, ability to handle heavy-duty tasks, higher precision, and longer lifespan are all advantages of using commercial-use blades.
Hobby Use
Cost-Effectiveness
Hobbyists usually prefer blades that offer good performance at a more affordable price point. These blades might not have the same longevity as commercial ones, but they are cost-effective for less frequent use.
Ease of Use
Blades for hobbyists are generally designed for ease of use and versatility, to accommodate a range of materials and projects typically encountered in home settings.
Size and Compatibility
Hobbyist blades are often made for smaller, more portable saws that are suitable for home workshops and less intensive tasks.
Advantages
They are affordable, suitable for a variety of light to medium tasks, easy to handle and change, and compatible with commonly used home tools.
Both commercial and hobby blades have their specific advantages, and the best choice depends on the demands of the projects, frequency of use, and the desired investment in blade quality.
Discover the Fastener Systems Difference Today
Experience the difference that comes with top-tier tooling solutions tailored to your unique needs. At Fastener Systems Inc. (FSI), we pride ourselves on offering products that enhance your efficiency while ensuring maximum durability. Don't compromise on your project's quality—start building better today with Fastener Systems.
Contact us today for more information!