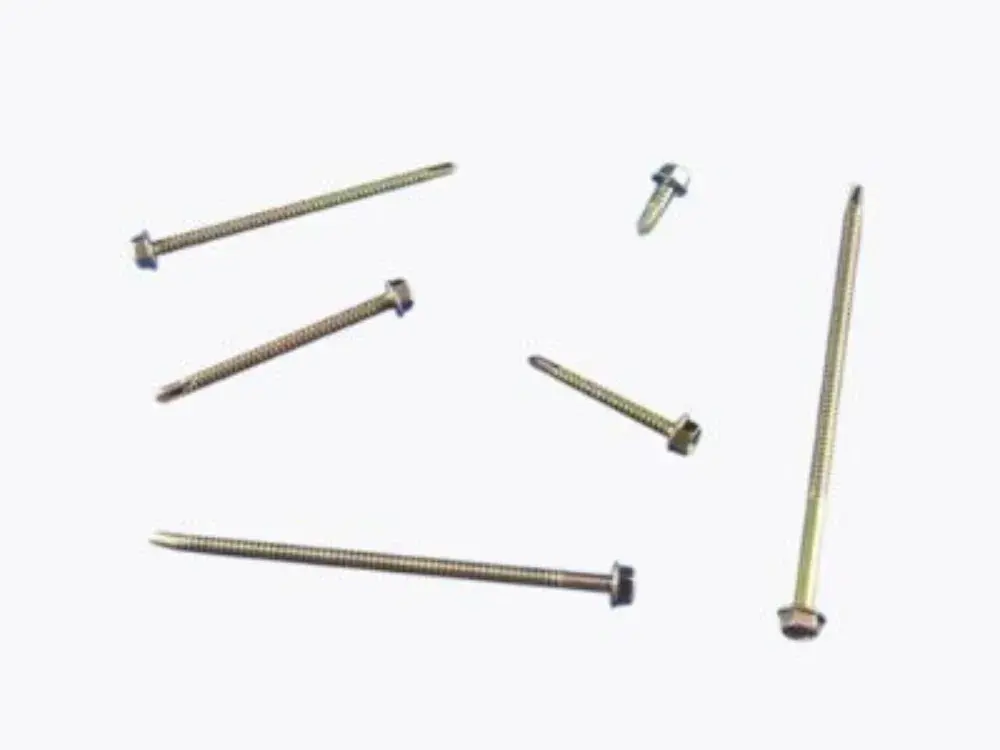
The type of fasteners used in construction projects is important because it can impact the project's success as much as the materials and methods selected. Many professionals in the construction industry wonder whether zinc-plated screws rust, particularly when used in outdoor settings.
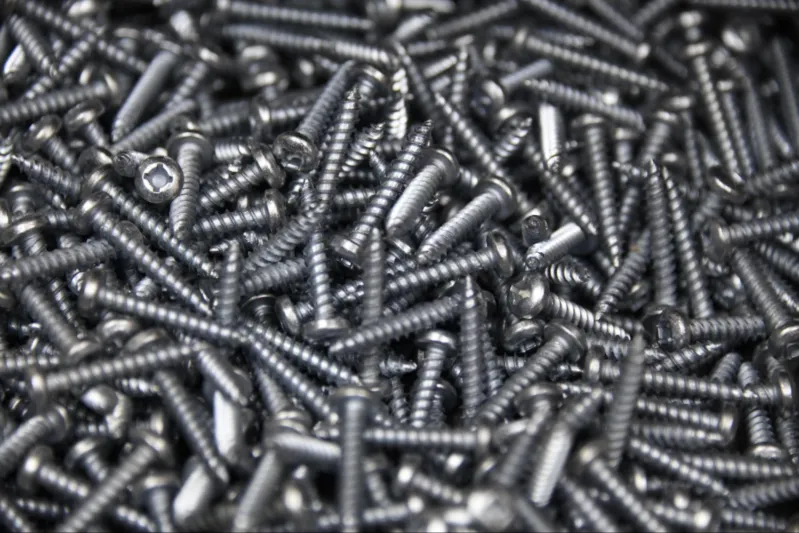
This article will explore the possible uses of zinc-plated screws and clarify any misconceptions surrounding them.
Zinc-Plated Screws and Their Applications
Zinc-plated screws are popular fasteners known for their corrosion resistance properties. They undergo either galvanization or electroplating with zinc to create a protective layer that makes them suitable for various applications.
What About Yellow Zinc Screws?
Yellow zinc screws are screws that have been zinc-plated and then given a chromate conversion coating. The coating adds a yellow coloring to the screws and provides an extra layer of protection against corrosion to make them even more long-lasting.
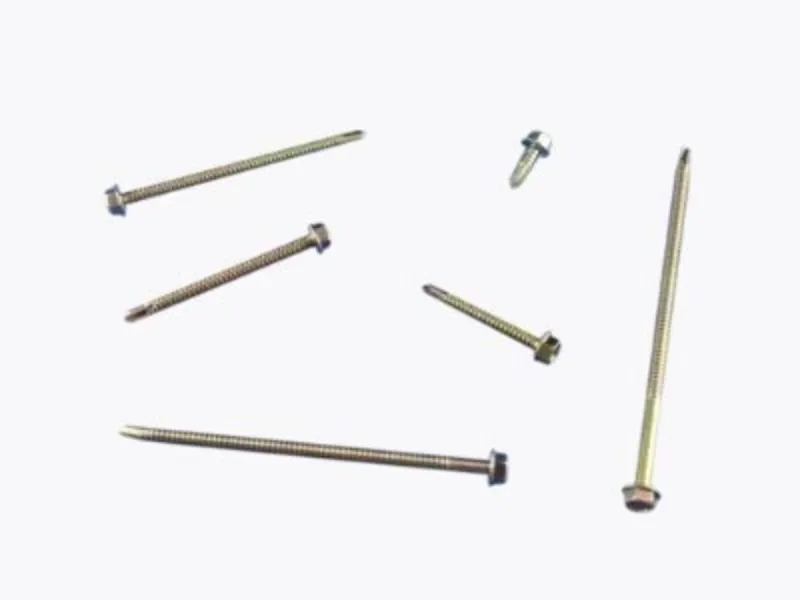
Electroplated Screws: Using Electricity to Bond a Protective Layer
Electroplated screws are manufactured with an electrical process where a thin layer of zinc is bonded onto the stainless steel screw's surface, in order to provide effective corrosion resistance while maintaining a sleek appearance. It should be emphasized that although zinc plating helps prevent corrosion, zinc itself will eventually corrode. The corrosion rate depends on both the thickness of the coating and the environment where the screws are used.
Overall, zinc-plated screws are a cost-effective option for many applications that provide corrosion resistance and durability.
Corrosion Resistance Properties of Zinc Screws
Zinc-plated screws, whether galvanized or electroplated, offer excellent corrosion resistance due to the protective outer layer of zinc. Zinc's corrosion rate is much slower than other metals such as iron or aluminum, for superior protection.
Formation of an Oxide Barrier on the Screw's Surface
The key factor behind the superior corrosion protection is the formation of a thin oxide layer on zinc's surface when exposed to air or moisture. This barrier prevents further oxidation and protects the underlying steel from rusting.
Comparison with Other Metals' Corrosion Resistance Properties
Stainless steel screws, for instance, have good corrosion-resistance qualities; yet in some scenarios their zinc equivalents may be more cost-effective.
Preventing White Rust Issues in Zinc-Coated Fasteners
Despite the corrosion resistance properties of zinc screws, they may still encounter white rust issues. White rust occurs when humidity gets trapped between surfaces coated with fresh electroplating layers.
Causes behind white rust formation
- Inadequate drying after plating process
- Poor packaging or storage conditions
- Lack of proper air circulation around the fasteners during transportation and installation
Remedies for dealing with white rust issues
To prevent and treat white rust on zinc-coated fasteners, consider these solutions:
- Exposure to free-flowing atmosphere: Allowing affected areas to breathe can help minimize moisture buildup.
- Clean off loose material: Lightly brushing away any loose particles and then wipe down with a clean dry cloth to restore the original appearance of your screws.
Hot-Dipped Galvanized Screws for Exterior Use
If you're working on an outdoor project like a deck, it's important to choose the right fasteners that can withstand harsh weather conditions. Hot-dipped galvanized screws are an excellent choice because they provide superior corrosion protection.
What is Hot-Dip Galvanization?
Hot-dip galvanization is a process where steel or iron components are dipped into molten zinc to create a protective coating. The zinc reacts with the underlying steel to form a series of intermetallic layers that provide exceptional corrosion resistance.
How Does Zinc Protect Against Corrosion?
Zinc corrodes at a much slower rate than steel, so when it's used as a coating on screws and other metal parts, it protects against rust and other forms of corrosion. If the outer layer of zinc gets scratched or damaged in any way, the underlying layers will continue to protect against rust formation.
Differences Between Zinc Plating and Hot-Dip Galvanizing
- Zinc plating involves electroplating thin layers of zinc onto metal parts while hot-dip galvanizing requires dipping entire components into molten zinc.
- The thickness of the coating produced by hot-dipping is typically thicker than that achieved through electroplating (upwards from 50 microns).
- The silicon bronze screw alloy contains copper which resists saltwater damage better than stainless steel, but has less strength compared with stainless-steel screws; hence its use in marine applications such as boat building and dock construction among others.
Zinc corrodes before the underlying steel, by sacrificing itself to protect the steel. However, zinc plating is not foolproof, and over time, it can wear away, leaving the steel exposed and vulnerable to rust.
Tips for Using Zinc Screws Effectively
Following some best practices will make sure you get the best use from zinc screws. One important step is test-driving sample screws in the material you intend to use, which helps identify any potential issues before committing to a large-scale project.
- Selecting the right screw type based on application: Opt for larger gauge screws when driving into hard materials like hardwood or concrete.
- Additionally, consider using square-drive or star-drive recesses as they resist stripping better than Phillips head or combination Phillips/square recesses.
Choose Fastener Systems Inc. for Your Zinc-Plated Screws
When it comes to sourcing quality zinc-plated screws that can withstand the test of time, look no further than Fastener Systems Inc.. We offer a wide range of fasteners, including zinc-plated and yellow zinc screws, known for their durability and resistance to rust. Our products are designed to meet the demanding needs of various industries, including construction, automotive, and electronics.
Contact us today to learn more and to get a quote on your next project!