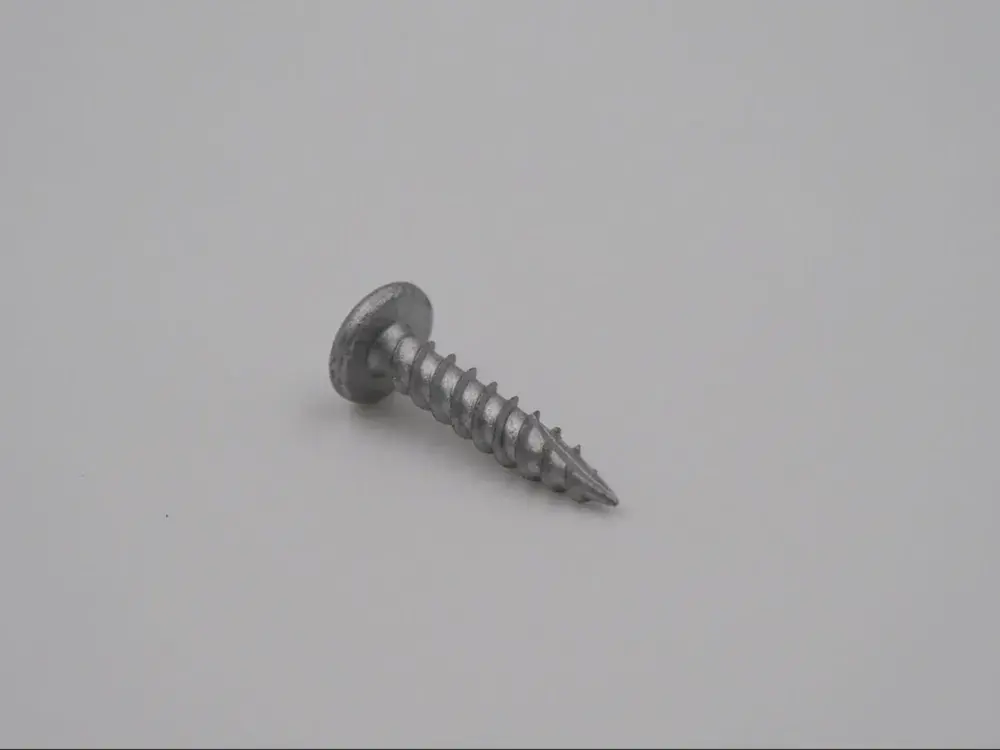
Self-tapping screws are a versatile and reliable fastening solution for many assembly projects. They offer the convenience of being able to form their own threads while being driven into pre-drilled holes, which reduces the need for additional tools or materials.
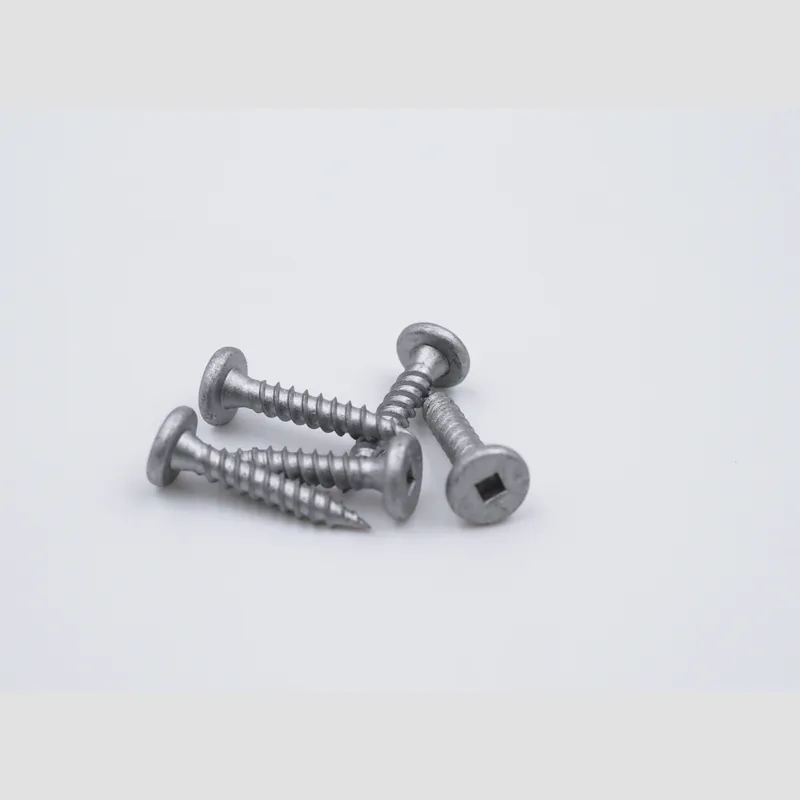
However, not all self-tapping screws are created equal. In this article, we’ll discuss how to use self-tapping screws in different materials so you can make an informed decision on which type is best suited for your project!
Understanding Self-Tapping Screws
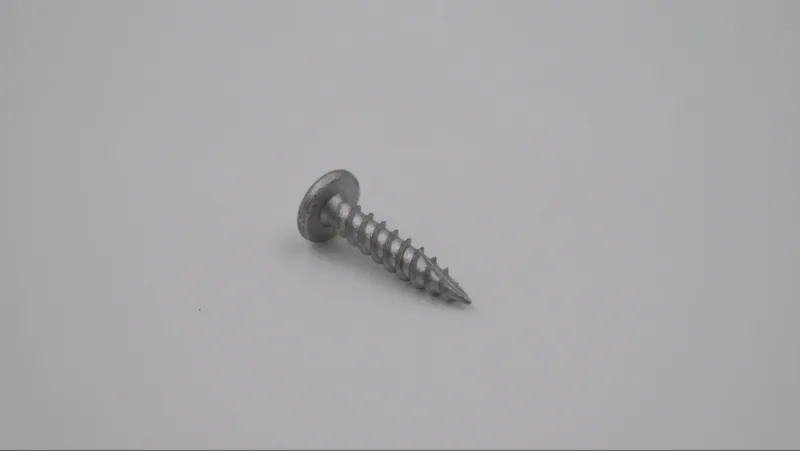
Self-tapping screws stand out due to their ability to create threads while being installed into a pre-drilled hole. Essentially, self-tapping screws carve their own route, which is the reason for their "self-tapping" label. Their standout feature is their capability to secure items together without the need for nuts or pre-formed threads, to make assembly tasks more streamlined.
Self-tapping screws are available in two versions:
- Thread-Forming
- Thread-Cutting
Thread-Forming Screws
Thread-forming screws are also known as "plastic" screws because they're predominantly used in soft materials like plastic, nylon, or other thermoplastics. They are characterized by:
Displacement of Material: Unlike their thread-cutting counterparts, thread-forming screws don’t remove any material. Instead, they push or displace it, which creates threads in the process.
Minimal Damage: Thread-forming screws displace rather than cut material, so they minimize the risk of splitting or cracking the material. This is particularly beneficial when working with delicate or brittle materials like plastic.
Tight Fit: Thread-forming screws usually create a snug fit because the displaced material tends to rebound and fill in the space between the screw threads, to help ensure a secure connection.
Thread-Cutting Screws
Thread-cutting screws are designed for use in hard materials such as metal or hard woods. They have a unique feature:
Material Removal: Thread-cutting screws are different from thread-forming screws because they cut threads into the material as they are driven in, which removes material as they go. Thread-forming screws do not remove material.
Reduced Stripping Risk: By cutting away material, they reduce the risk of the material stripping under the pressure of the screw being driven in.
Versatility: Thread-cutting screws can be used in a wider range of materials than thread-forming screws, including metals and hardwoods.
Self-Tapping Screws are Available for Different Uses
Sizes
Self-tapping screws come in different sizes, and the sizes are usually indicated by a number from 0 to 24, which represents the diameter of the screw. Common sizes include:
- No. 2, No. 4, and No. 6 for small applications like delicate carpentry or electronics.
- No. 8, No. 10, and No. 12 for medium-sized applications like securing medium-density materials.
- No. 14 and above for heavy-duty applications like construction or machinery assembly.
Styles
Pan Head: These screws have a slightly rounded top and vertical sides, which allows them to bear a good load.
Flat Head: Flat head screws have a flat top that allows them to be driven into the material until they're flush with the surface.
Oval Head: Oval head screws are a combination of flat and pan head screws. They're driven in like flat head screws, but have a slightly rounded top like pan head screws.
Hex Head: Hex head screws have a hexagonal top that allows them to be driven in with a wrench.
Truss Head: Truss head screws have a rounded top with a large, flat underside. They provide a large bearing surface and are used in applications where minimal deformation is desired.
Bugle Head: Bugle Head screws have a 'bugle' shape which is curved downwards from the head to the shank. They're commonly used in woodworking and for attaching plasterboard.
Always match the size and style of the screw to your project for a successful outcome.
How to Install Self-Tapping Screws
Here is a step-by-step guide:
Step 1: Choose the Right Screw and Tools
Firstly, identify the type of material you're working with and choose the appropriate self-tapping screw. As stated earlier, thread-forming screws are suitable for plastics while thread-cutting screws are for metal and wood. Ensure you have a power drill with a screwdriver bit that fits the head of your screw.
Step 2: Pre-drill a Hole
Be sure that the pre-drilled hole is slightly smaller than the diameter of your screw, so that the threads can engage properly.
Step 3: Position the Screw
Make sure the screw is perpendicular to the material to ensure it goes in smoothly and reduces the risk of stripping the screw head.
Step 4: Drive the Screw
Using a power drill or a manual screwdriver, slowly drive the screw into the material. Apply a steady pressure and maintain a consistent speed to prevent damaging the material or the screw.
Step 5: Check the Fit
The screw should be flush with the material surface, and there should be no movement in the joint.
Using Self-Tapping Screws in Plastic
For plastic, it's better to use thread-forming screws because they push the plastic aside instead of cutting through it, to minimize the chance of cracks or damage.
Be careful about the drilling speed and pressure to avoid overheating or over-tightening.
Achieve Superior Results with Fastener Systems Inc. Self-Tapping Screws!
Fastener Systems Inc. has a variety of self-tapping screws including thread-forming and thread-cutting options that cater to your project needs. Our high-quality fasteners and tools provide dependable backing for your assembly tasks.
Contact us today for more information and a free quote for your upcoming project!