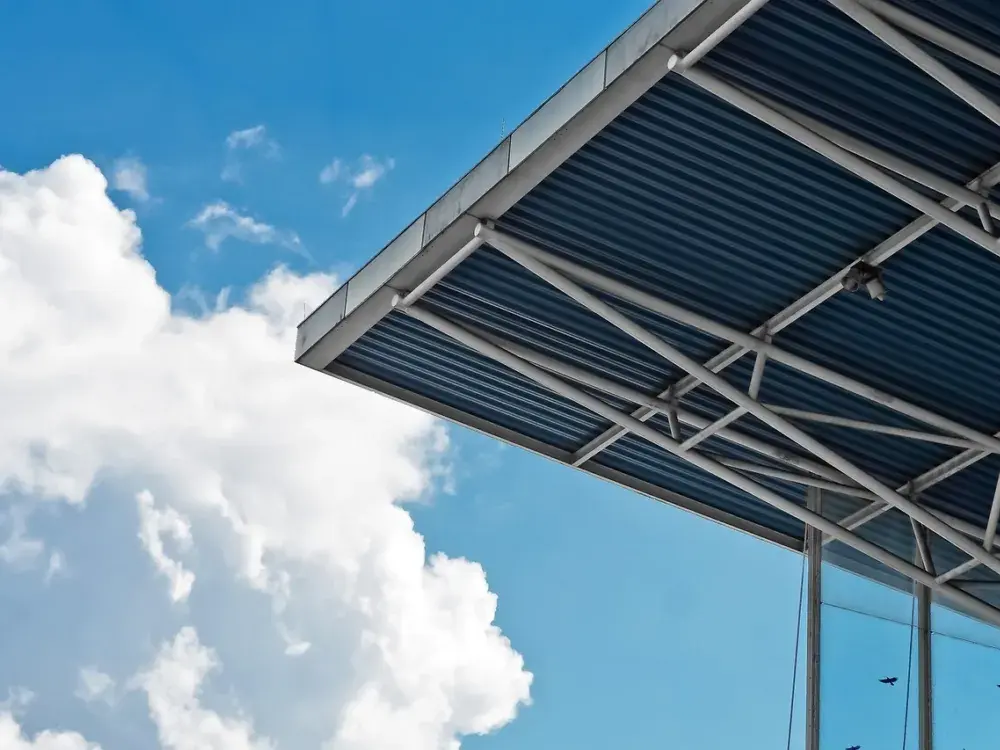
If you're thinking about using metal roofing for your next project, it's essential to select the appropriate screw size. Using the wrong size screws can lead to problems such as moisture infiltration, weakened roof structure, and invalidation of product warranties.
This article will discuss the most frequent screw sizes for metal roofs and provide some guidelines on how to choose the right one for your project.
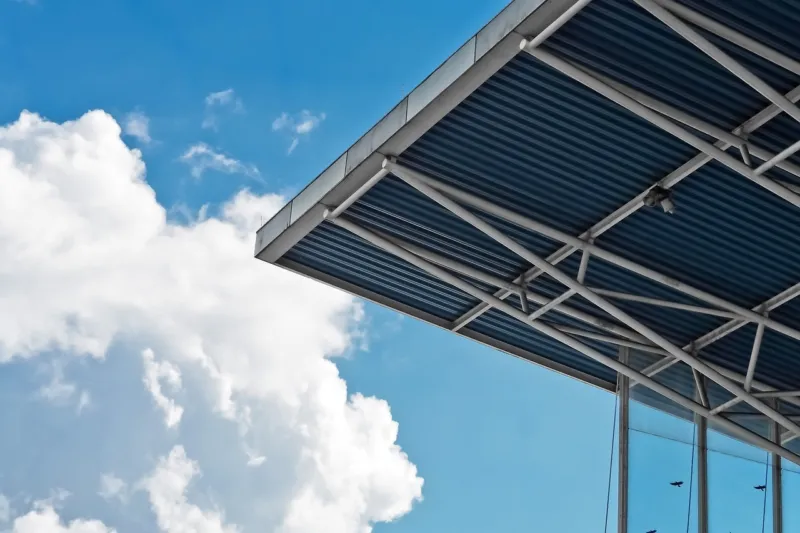
Understanding Metal Roofing Screws
Metal Roofing Screw Anatomy
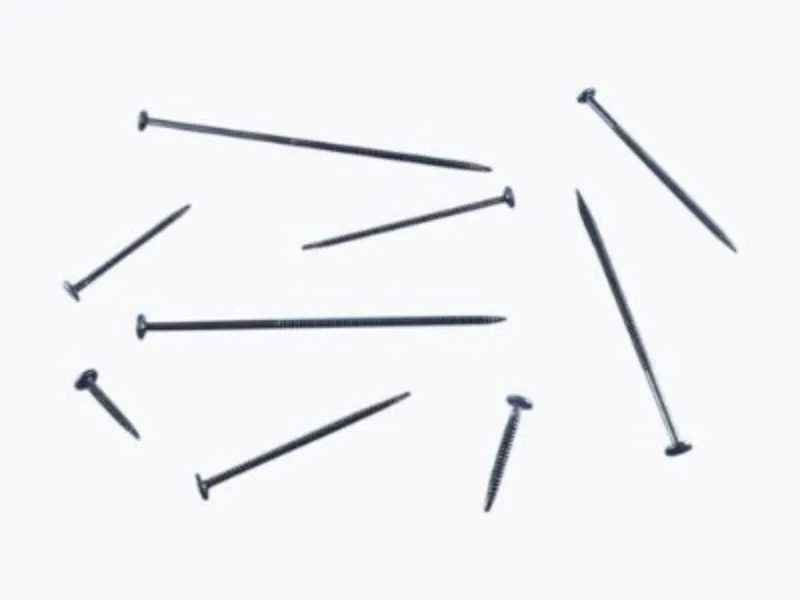
A typical metal roofing screw is made up of two main parts: the head and the shank. Metal screws are designed with additional features such as a sealing washer to prevent water penetration and a corrosion-resistant coating, and they are available in different colors to match your roof. Their drill points are designed to enable faster penetration into wooden or metal substrates.
The Importance of Screw Size
To specify a metal roofing screw, you need to consider its three components: shank diameter (not the diameter of the screw head), number of threads per inch, and length. For instance, a #12-14 metal roofing screw has a diameter of #12 and 14 threads per inch.
Common Screw Sizes for Metal Roofs
1 1/2-inch Screws
For metal roofing projects, it's typical to use 1 1/2-inch screws with a 1 1/4-inch depth to securely fasten the panels. If the roofing sheets are thicker, sizes such as 1-inch or 2-inch screws may also work.
2-inch Screws
To ensure proper installation, use 2-inch screws for roofing projects that involve overlapping panels or 7/8-inch corrugated panels. These screws are long enough to penetrate two panels and provide enough depth in the substrate.
1-inch Screws
For standing seam roofing projects, the standard screw size is 1 inch. These screws can securely hold by penetrating up to 3/4 inches into the substrate.
Other Considerations When Choosing the Correct Screw Size for Metal Roofing
Choosing the correct screw for your metal roofing involves several factors, including the type of panel system, screw colors, screw coating and material, screw length, type of screw needed, drill points, screw sizes, head types, and thread count.
Exposed fastener panels require fasteners with rubber washers for weather resistance and to block water. For concealed roofing panels like standing seam or flush wall panels, select fasteners with a low-profile head to prevent contact with the underside of the roofing panel.
Fasteners are available with color-coated heads to match the color of your metal panels to create a neat appearance since metal panels and screws come in various colors.
To avoid galvanic action caused by dissimilar metals in contact with moisture, it's important to choose screw materials and coatings that are compatible with your metal roofing and siding. For instance, use stainless steel type 304 screws with matching paint color on the heads for aluminum roofing and stainless steel type 410 screws that are copper-plated for copper roofing.
Make sure the fasteners you use are long enough to go through all the material. Ideally, the screws should penetrate at least 3/4 inch into the material you're fastening to. Keep in mind that longer screws may create more twisting force while driving, which could cause them to break during installation.
To determine the right screws for installation, you need to consider the surface they will attach to. When working on a residential plywood roof, the preferred screws are metal to wood roofing screws. However, for commercial or agricultural projects, the screws can be attached to wood, light gauge metal purlins, or heavy steel I-beams.
Self-drilling screws, also called Tek screws, are commonly used in metal-to-metal applications. These types of screws feature a drill-bit like tip that enables them to create their own hole and form mating threads. By doing so, they eliminate the need for pre-drilling and make projects quicker to accomplish.
What Happens When You Choose the Wrong Screw Size?
Selecting the correct size metal screw is critical in the proper installation of metal roofing due to several reasons as explained below:
The metal screws serve as fasteners that hold the metal panels securely in place. If the screws are not fastened properly, they can work themselves loose over time, which might cause the metal roofing to be less stable and durable.
The correct installation of screws is essential for preventing moisture intrusion. Each fastener site is a potential source of water leakage if not handled correctly. Over tightening or under tightening the screws can lead to leak points and cause water damage inside the property. Correct tightening creates a proper seal for the washer and prevents leaks.
Installing the screws straight and flush creates the proper washer seal and reduces the risk of leaks. Screws driven in at an angle might not create an effective seal and therefore, can lead to potential leakage.
Fastening screws should be done in accordance with the metal roofing manufacturer’s instructions to maintain the warranty of the product. Incorrect fastening not only increases the risk of roofing problems, but also potentially nullifies the product warranty.
Depending on the roof design, putting screws in certain places can reduce the risk of the screws pulling out during wind events, thereby maintaining the roof's structural integrity.
When metal screws are correctly installed, they contribute to the durability and longevity of the roof. A well-installed metal roof can last a lifetime or even longer, and reduce the frequency of roof replacements.
Ensure Long Lasting Metal Roof Installations with Metal Screws from Fastener Systems
Fastener Systems Inc. offers top-of-the-line metal roofing screws in a variety of sizes, coatings, materials, head types, drill points, and thread counts to ensure your project is successful. You can trust that our products meet the highest standards and offer superior performance.
Contact us today for a catalog of our complete product line!