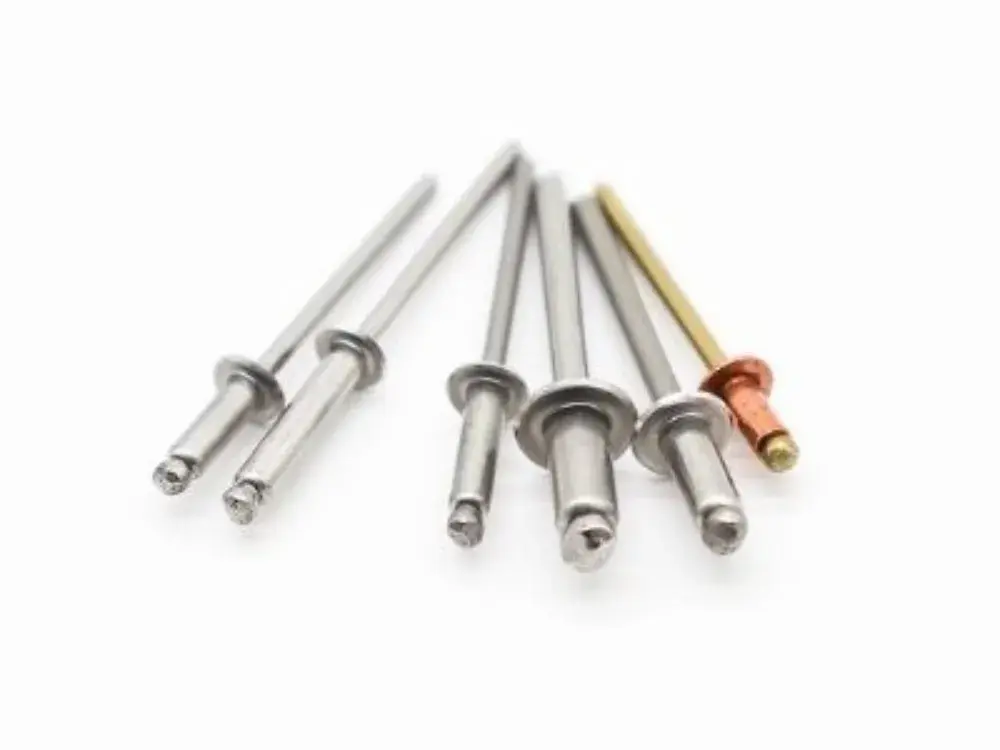
Rivets have been used for centuries to secure different materials, and they have evolved from a simple tubular rivet design into the modern pop rivet. Pop rivets are much easier to install than traditional rivets, because you only need access to one side of the material, so it makes them a popular choice in many industries.
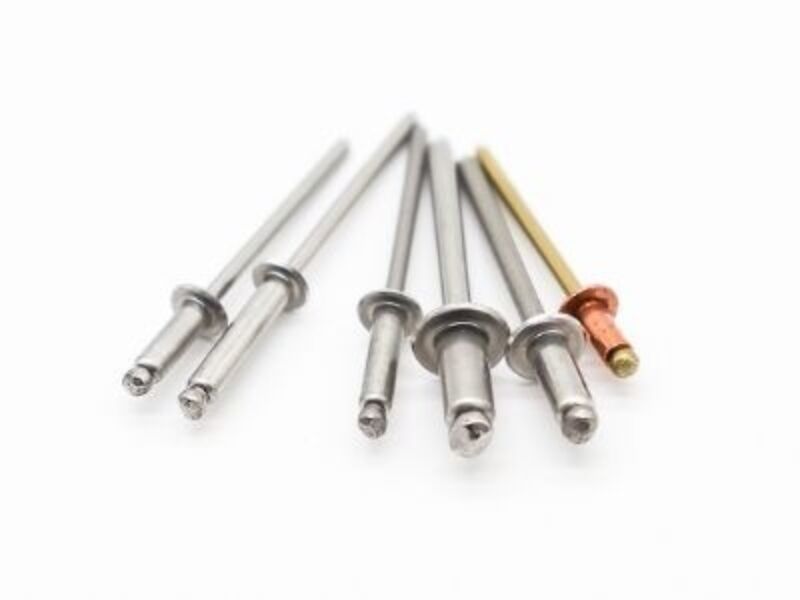
Painted aluminum pop rivets offer even more advantages than just ease of installation. They can also provide an attractive finish to your project, while still providing superior strength and durability. With painted pop rivets, you get both an aesthetic appeal and a strong connection that will last for years.
What Are Rivets and Why Were They Invented?
For centuries, rivets have been one of the most reliable materials to securely join two elements. From Ancient Egypt's clay jars with handles, up to the height of Rome when they were widely used in construction projects - their applications and use only increased over time. For more than 5,000 years, people have employed them as a crucial resource for many purposes.
The idea behind the rivet is simple: a solid cylindrical pin is inserted through two metal plates to hold them securely together. This process was first used by blacksmiths in the Middle Ages and was known as a hot rivet.
The process involves feeding bright red-hot rivets into precisely created holes, where the unfinished end is then struck to seal up the bond. As it cools down, this causes shrinking and tightening of the joint, completely. Riveting has been extensively used throughout history in many industries:
- Pre-engineered metal buildings
- High-rise steel buildings
- Boat building
- Aircraft construction
Their ability to provide a secure connection without welding or gluing, makes rivets essential components for many applications today. Unfortunately, rivets require access to both sides of the material to be properly utilized, which has limited their use.
Why Are Pop Rivets Needed?
The origin of the pop rivet began in England in 1916 with a fastener similar to today's pop rivet, but instead of self-sealing, the top part of the rivet was held in place by a nut.
A new tool, the pop rivet gun - allowed for installation and securing of the rivet in one action - without the need for a nut or any other product to hold it in place.
A pop rivet - commonly known as a blind rivet – is a unique type of fastener ideal for applications with limited or nonexistent access to the rear side (hidden) of components. It consists of two essential pieces: an outer shell, otherwise termed the "rivet body" or “hat”; and an inner stem referred to as a mandrel. When both sides cannot be accessed during installation, simply drill through each section to accommodate your pop rivet.
After you drill a hole in your parts, place the rivet body into contact with them, and then use a pop rivet gun to pull the mandrel into it. This causes the rivet body to expand and grip both pieces tightly together - permanently joining them at that localized joint. The mandrel will snap off once everything is secure; no further action is required.
Pop Rivets Have a Wide Array of Uses
These are just a few of the many uses for pop rivets:
- Securing sheet metal and other lightweight materials
- Joining two pieces of wood or plastic together
- Fastening separate accessories to a machine or car frame
- Connecting gutters to downspouts
- Repairing automobiles and other motorized vehicles
- Attaching fabric or vinyl awnings to structures
The Benefits of Custom Painted Aluminum Pop Rivets
Painted pop rivets are an economical and aesthetically pleasing alternative to plain, unpainted metal fasteners. For many hardware applications, painted rivets are an excellent choice because they can easily match surrounding colors and designs while also providing additional protection against corrosion.
They also reduce installation time, as they are easier to install than other types of rivets that require additional painting after they have been installed.
Fastener Systems, Inc. Provides the Painting Solution
Our system is based on three criteria:
- Color match
- Even paint coverage
- Durable finish
Step by Step Process
There are several steps in the process that must be followed exactly to produce the most resilient custom-painted pop rivets:
- Obtain a color chip for the painter to match.
- The rivets are racked in a grate with holes properly sized so the fastener faces head up. They are spaced close enough to minimize paint usage, but not too close that even coverage is hindered.
- The racked pop rivets are put in a large blasting machine where different levels of blasting occur, depending on the finish of the part. For example, stainless steel would see more blasting time than a carbon steel coated part.
- The still racked pop rivets are blown clean.
- They are sprayed with a primer.
- Afterwards, they are painted with a proprietary paint.
- The pop rivets are baked in a walk-in oven at a specific temperature for a specific amount of time
- Finally, the parts are allowed to cool down and cure.
Quality Control Ensures the Pop Rivets Meet Our Demanding Standards
During this time, an experienced manager visually examines the painted items, by comparing the original color chip to the finished product for accurate match and paint coverage around all sides of the fastener, and then performs a “Tape Test” which has a procedure of its own.
- The pop rivets go through a soft de-racking on a carpet surface to minimize chipping.
- Retained samples are kept for documentation and future reference.
- The final product is carefully packaged with thick packing paper to minimize chipping during the shipping process.
Discover the Benefits of Custom Painted Aluminum Pop Rivets from Fastener Systems, Inc.
For quality custom painted fasteners and pop rivets at competitive prices, look no further than FSI. Our superior painting process ensures reliable results that last, while our extensive selection of colors guarantees our fasteners will match your project. In addition to providing premium products, we also provide exceptional customer service.
Our team is available to answer any questions you have, so you can keep your projects moving forward.
Contact us today to learn more or get a quote!