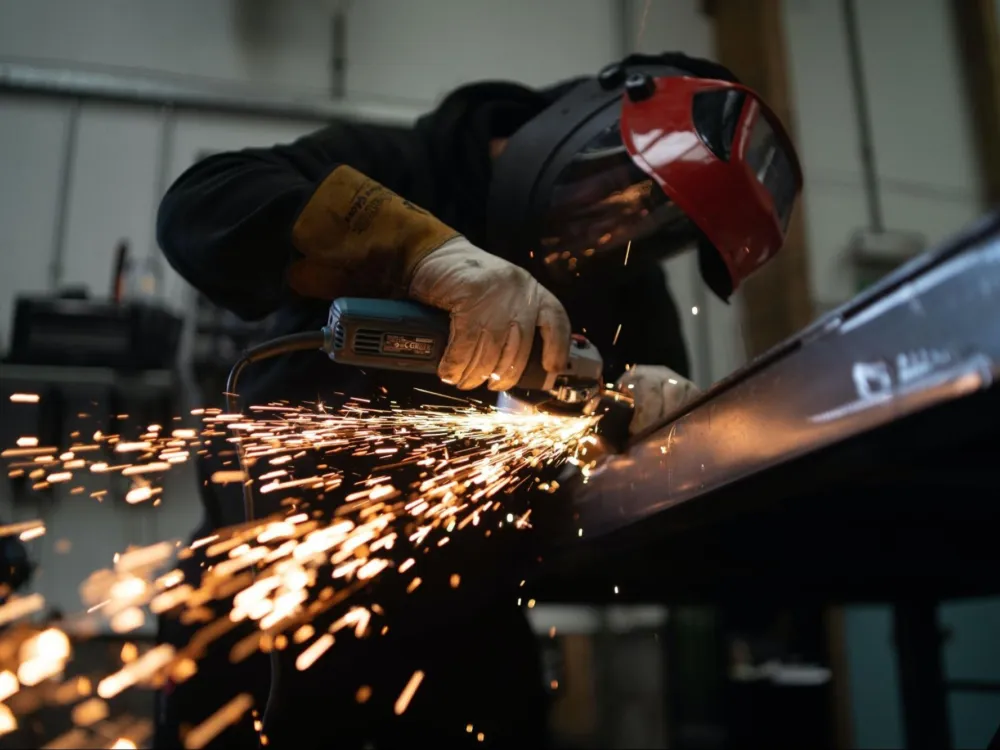
Grinding is an essential part of metalworking, and metal grinding wheels are a key component in any workshop. Whether you’re cutting, shaping, or smoothing metal surfaces, the right grinding wheel can make all the difference in achieving a high-quality finish. This article will provide you with the knowledge you need to select the best metal grinding wheel.
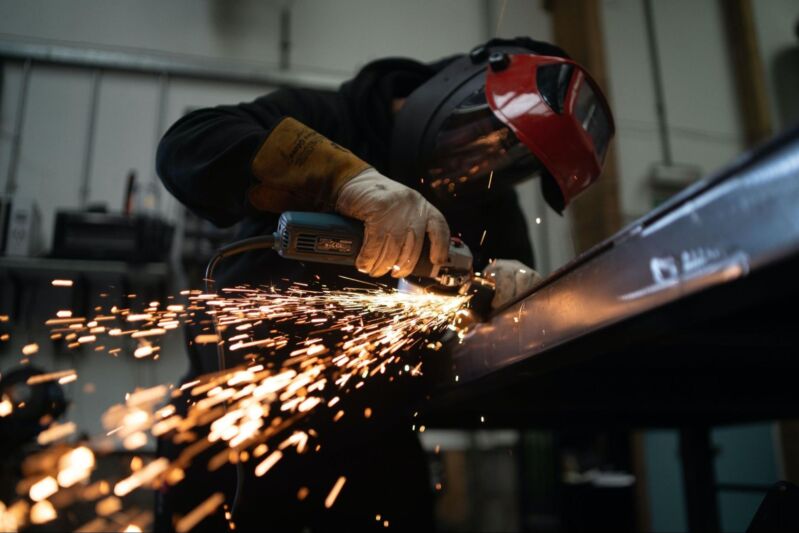
What Are Metal Grinding Wheels?
Metal grinding wheels are abrasive wheels used for grinding, cutting, and shaping metal workpieces. Grinding wheels are typically made with a bond that holds abrasive grains together and a variety of abrasive materials are used to create different grades of wheels for different applications. The wheels are available in various shapes, sizes, and compositions to meet specific grinding requirements.
Metal grinding wheels are commonly used in metal fabrication, maintenance, and welding applications to remove excess material from metal workpieces, smooth out rough edges, and create a polished finish.
Types of Metal Grinding Wheels
The type of grinding wheel you need will depend on what type of metal you’re working with and what kind of finish you want to achieve. Generally speaking, there are three main types of grinding wheels:
- Cut-off wheels
- Roughing wheels
- Finishing wheels
Cut-off wheels are designed for fast stock removal while roughing wheels are used for heavy material removal. Finishing wheels are used for polishing or blending surfaces to create a smooth finish.
Factors to Consider When Choosing a Grinding Wheel
When it comes to choosing the best metal grinding wheel for your project, there are several factors to consider such as type, grit size, bond strength, wheel hardness, and application type.
Bonding Material
Grinding wheel bonding materials play an essential role in determining the grinding wheel's properties, including strength, durability, and cutting efficiency. There are various bonding materials used in grinding wheels.
Vitrified Bonds
Vitrified bonds are one of the most commonly used bonding materials in grinding wheels. They are made of a mixture of clays and feldspars that are heated to high temperatures to create a glass-like bond. The vitrified bond provides excellent strength and rigidity, which makes it ideal for precision grinding applications.
Resin or Resinoid Bonds
Resin is another popular bonding material used in grinding wheels. Resin bonds are made from synthetic resins mixed with abrasive grains and fillers. They offer excellent cutting properties, which makes them ideal for grinding applications requiring high stock removal rates. Resin bonds are also flexible and can absorb shock, so they are ideal for grinding applications involving high vibration.
Silicate Bonds
This type of bonding material is used in grinding wheels and it contains a mixture of silicate and clay. Silicate bonds are used in applications that require low cutting forces and high precision, which makes them ideal for grinding applications that require a smooth surface finish.
Shellac Bonds
Shellac bonds are made of natural resins and they are primarily used in small grinding wheels. Shellac bonds are typically used in applications that require high precision and low cutting forces, such as sharpening tools.
Rubber Bonds
This type of bond is used in applications that require high elasticity and vibration damping. Rubber bonds are ideal for grinding applications that involve delicate workpieces or materials that are prone to cracking or breaking under stress
Types of Grinding Wheels
Type 27
These wheels have a flat profile and indent in the center, so they are an optimal choice for stock removal between 25-35 degrees. Furthermore, they are exceptionally effective even when used at angles up to 45 degrees.
Type 28
Type 28 wheels feature a concave design that allows them to perform best at angles between 0 and 15° from the surface. This type is ideal for those who need to access narrow spots or require more aggressive working angles.
The Best Metal Grinding Wheels By Their Design
The grains used in grinding wheels are the key to their functionality. The following examples of grains can be found in the various grinding wheels on the market. It's also possible to mix some of these elements for more specialized results.
Ceramic Alumina
Ceramic alumina grinding wheels are especially useful for applications where high accuracy and surface quality are required. These include: tool and die making, medical device manufacturing, aerospace components, and automotive parts production.
Ceramic alumina grinding wheels offer superior performance compared to conventional aluminum oxide abrasives due to their higher strength and hardness as well as their greater resistance to wear and tear.
Zirconia Alumina
With zirconia alumina grains, you get a powerful combination of both speed and durability. This self-sharpening grinding material performs superbly on metal surfaces such as steel and stainless steel, even under heavy pressure or extreme temperatures.
Zirconia Alumina Blended with Ceramic Alumina
Zirconia alumina blended with ceramic alumina is an ideal material for grinding wheels due to its high hardness, strength, and wear-resistance. This combination of materials provides a durable wheel that can be used for a variety of applications. Its high melting point makes it a perfect choice for use in grinding wheels that will experience extreme heat during operation. The addition of ceramic alumina increases the hardness and wear resistance of the wheel, in order to allow it to withstand more aggressive grinding operations.
White Aluminum Oxide
It is an angular, durable, and hard material that can be recycled multiple times without losing its cutting edge. It is also known for its high heat resistance, which makes it suitable for use in high-speed grinding applications. White aluminum oxide has a wide range of uses including grinding, polishing, lapping, abrasive blasting, and anti-slip aggregate. It is often used to grind metals such as steel and stainless steel as well as other materials like glass, stone, and plastic.
Aluminum Oxide
Aluminum oxide grains are the perfect tool for grinding steel, iron, and other metals. Its hardness makes it a fast initial cut option, yet its efficiency diminishes over time in comparison to wheels made with other types of grain - which often have higher longevity.
Silicon Carbide
Abrasive and fast-acting, silicon carbide is an ultra-hard grain that offers quick cutting but lacks the toughness of other grains.
Silicon Carbide/Aluminum Oxide Blend
For the best grinding experience on aluminum and other soft metals, a wheel composed of both silicon carbide and aluminum oxide is the ideal choice. The combination of these two substances results in quality cut rates that are faster than average, while also providing an extended lifespan for alloys such as aluminum.
Choose Fasteners Systems, Inc. for Your Grinding and Cutting Wheel Needs
If you're looking for the best metal grinding wheels for different materials, look no further than Fastener Systems, Inc. Our selection of grinding and cutting wheels provides you with the best options to complete your project quickly and with professional results.
Contact us today, or order a catalog to see our extensive lineup of fasteners, sealants, and tools.