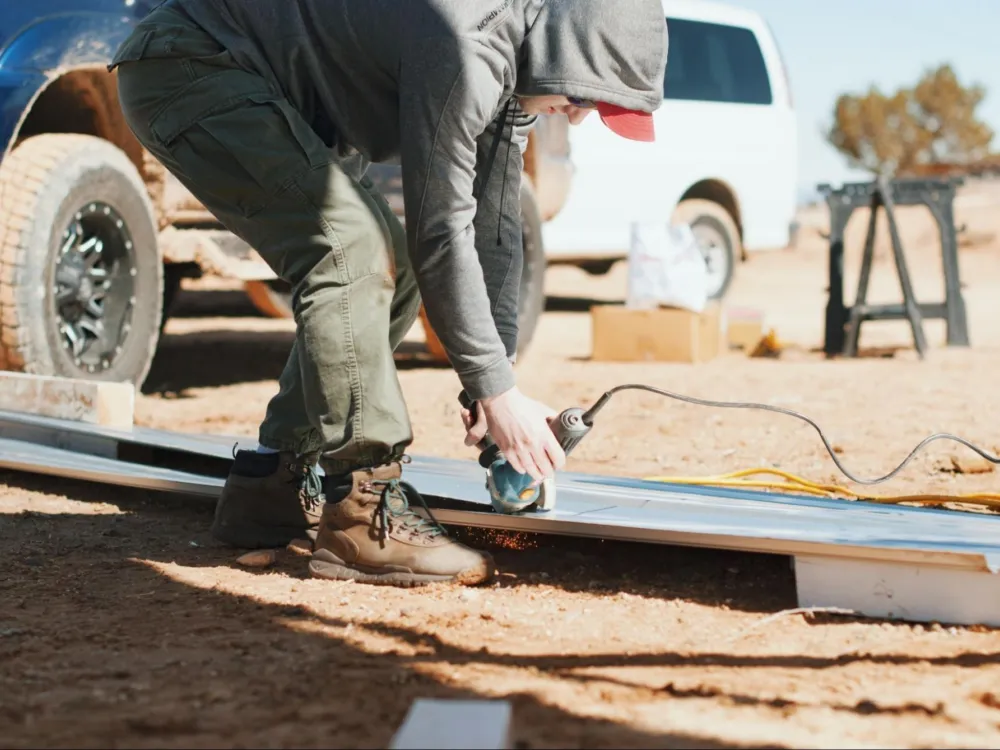
Metal cutting is a vital skill in many industries, including construction and DIY projects. The metal cutting wheel is a key tool for achieving efficiency and precision. This guide provides valuable insights for both beginners and experienced professionals in the world of metal cutting wheels.
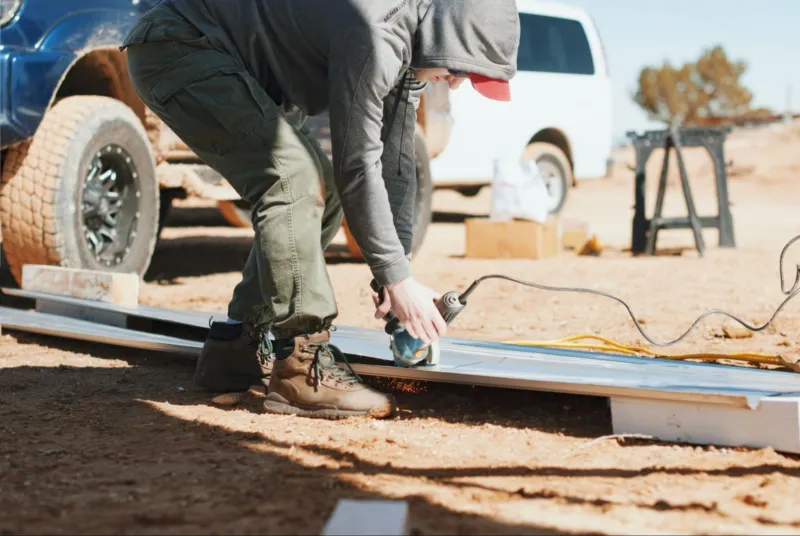
Understanding the Importance of Metal Cutting Wheels
Metal cutting is a critical process in various industries, including construction, automotive, and manufacturing. The use of metal cutting wheels is pivotal in these sectors for efficient, precise, and safe cutting of metals.
These wheels, whether abrasive or diamond, are essential for cutting through different types of metal, which can impact the overall quality and speed of work in both professional and DIY contexts. The metal cutting wheel is a key tool that determines the effectiveness of metalworking tasks, which makes its understanding and selection crucial for successful outcomes.
Types of Metal Cutting Wheels
Abrasive Wheels
General Characteristics: Abrasive wheels are made from abrasive particles bonded together. Common materials include aluminum oxide or silicon carbide.
Advantages: They are cost-effective and widely available, which makes them a popular choice for general-purpose metal cutting.
Best Uses: They are ideal for cutting softer metals like aluminum or for applications where fine precision is less critical. These wheels are suitable for quick, rough cuts in construction or basic metal fabrication tasks.
Diamond Wheels
General Characteristics: Diamond wheels feature industrial diamonds bonded to the wheel's perimeter. The diamonds are synthetic and are designed for high endurance.
Advantages: They are highly durable and can maintain their cutting ability for a longer period. Diamond wheels offer greater precision and are less prone to wear and tear.
Best Uses: They are perfect for cutting harder metals like steel or for tasks requiring high precision. They are commonly used in precision fabrication, automotive repairs, and detailed metalworking projects where precision is paramount.
Applications and Uses
Material Considerations: The choice between abrasive and diamond wheels largely depends on the metal type. Softer metals can be efficiently cut with abrasive wheels, while harder metals demand the resilience of diamond wheels.
Project Specificity: The nature of the project also guides the selection. For rough, quick cuts in a construction setting, an abrasive wheel is sufficient. However, for detailed, precision-based tasks in manufacturing or automotive industries, a diamond wheel is more suitable.
Machine Compatibility: Additionally, consider the compatibility with your cutting tools. Some wheels are designed specifically for certain machines, like circular saws or angle grinders.
Understanding the types of metal cutting wheels and their appropriate applications is crucial for achieving desired results. Whether working on a simple DIY project or a complex industrial task, selecting the right metal cutting wheel is the key to efficiency, precision, and safety.
Key Considerations in Metal Cutting
Types of Metals and Thickness
Metal Type
Aluminum: Softer and more malleable, aluminum requires a cutting wheel that can handle its gummy nature without clogging. Abrasive wheels with a finer grit are often preferred.
Steel: Harder and more durable, steel demands a cutting wheel that can withstand the material's resistance. Diamond wheels or abrasive wheels with coarser grit are ideal for cutting through steel efficiently.
Thickness of the Metal:
Thin Metals: For metals like sheet metal, a thinner cutting wheel is preferred as it reduces material loss and makes cleaner cuts.
Thick Metals: Thicker metals require wheels with greater durability and a deeper cutting capacity. A thicker, more robust wheel ensures stability and longevity during the cutting process.
Cutting Precision:
The precision required in your cut should also guide your choice. For detailed, fine cuts, a thinner, more precise wheel is essential. In contrast, for rough cuts, a standard wheel may suffice.
Cutting Speed and Wheel Wear:
Different metals and their thicknesses will affect the cutting speed and how quickly a wheel wears down. Softer metals may allow for faster cutting, but can wear down wheels quicker if the wrong type is used.
Heat Generation and Transfer:
Consider how the metal and its thickness will affect heat generation during cutting. Thicker metals tend to retain more heat and require a wheel that can handle high temperatures without losing integrity.
Precision vs. High-Speed Cutting
When choosing a metal cutting wheel, the decision between prioritizing precision or speed is significant. This choice impacts the type of wheel you use and how you approach the cutting process.
Precision Cutting
Characteristics: Precision cutting demands accurate, clean, and often intricate cuts. This is crucial in industries where detail is paramount, such as in aerospace or fine metalworking.
Wheel Choice: For precision cutting, thinner, finer-grit abrasive wheels or high-quality diamond wheels are preferred. These types of wheels offer better control and less material loss.
Considerations: When focusing on precision, the cutting speed is usually slower to maintain control and accuracy. The methodical approach ensures the cuts are exactly as required, to minimize errors and material wastage.
High-Speed Cutting
Characteristics: High-speed cutting is about efficiency and is often employed in situations like construction or bulk metal processing where time is a factor.
Wheel Choice: Thicker, coarser-grit abrasive wheels are typically used for high-speed cutting. These types of wheels can remove more material quickly, but might not leave as clean a cut as finer wheels.
Considerations: With high-speed cutting, there's a trade-off between speed and the finish of the cut. You can work through material faster, however the cuts might not be as precise or clean, and there's an increased chance of generating more heat and wear on the wheel.
Selecting the Right Metal Cutting Wheel
Material, Size, and Thickness
When selecting a metal cutting wheel, the material it is manufactured from is an important factor. The abrasive type used in the wheel affects its cutting capability. For instance, wheels made with aluminum oxide are typically used for cutting ferrous metals, while those made with silicon carbide are more suitable for non-ferrous metals.
Additionally, the durability and performance of the wheel are influenced by the bonding agents used. Commonly, resin-bonded wheels are chosen for their balanced cutting performance and strength.
The size of the wheel is another important aspect. The diameter of the wheel should align with the required depth of cut. Larger diameter wheels can make deeper cuts but might necessitate the use of more powerful machinery.
It’s essential to make sure that the wheel's arbor size is compatible with your machine's specifications in order to ensure a secure and safe fit.
Finally, the thickness of the wheel plays a crucial role. Thin wheels are preferable for making precise, shallow cuts and can help to reduce material wastage. On the other hand, thicker wheels are more durable and suitable for deep cuts and heavy-duty cutting tasks.
Compatibility with Machinery
When selecting a cutting wheel, it's important to consider the type of machinery you'll be using. Different wheels are designed to be compatible with specific machines, such as angle grinders or circular saws. Using a wheel that's not designed for your specific type of machinery can lead to suboptimal performance and may even pose safety risks.
The power output and revolutions per minute (RPM) of your machinery are significant factors in choosing the right wheel. A wheel must be able to handle the machine's power and speed. Using a wheel that's not rated for your machine's power output or RPM can be both dangerous and inefficient.
Finally, proper mounting and safety considerations are vital. The wheel should fit securely onto your machine to prevent accidents and ensure quality cuts. Additionally, it's important to check the wheel's compatibility with any safety guards or attachments that have been provided with your machinery.
Also, consider the specific application of the wheel, such as whether it's suitable for wet or dry cutting conditions, to ensure optimal performance and safety during the cutting process.
Techniques for Effective Metal Cutting
Approach and Cutting Angle
Understanding the Cutting Angle
The angle at which the wheel contacts the metal can dramatically impact the quality of the cut. An improper angle can lead to jagged edges, increased wear on the wheel, and even safety hazards.
A perpendicular angle (90 degrees) is generally the standard for many cutting tasks, and will help ensure an even and clean cut. However, specific tasks may require different angles for optimal results.
Adjusting the Angle
For thinner metals or precision cuts, a slight angle might be more effective in reducing the risk of the metal warping.
In thicker materials, a steeper angle can help initiate the cut more effectively before leveling out to a standard cutting angle.
Technique and Skill:
Mastering the approach and angle requires practice and skill, especially when dealing with varying thicknesses and types of metal.
Cutting Pressure and Speed
Optimal Cutting Pressure
Applying the right amount of pressure is crucial. Too much pressure can overburden the wheel and the tool, which can lead to premature wear and potential breakage. On the other hand, insufficient pressure can result in an inefficient cut and increased time.
The correct pressure should allow the wheel to cut through the metal without forcing it. This balance is key to achieving a clean cut and prolonging the wheel's life.
Managing Speed
The speed at which you cut (not to be confused with the RPM of the wheel) also plays a significant role. Moving too fast can cause the wheel to skip or jump, which can lead to an uneven cut, while moving too slowly can generate excessive heat and wear down the wheel.
Finding the right speed often depends on the type of metal, the thickness, and the type of cut required.
Consistent Application
Maintaining consistent pressure and speed throughout the cut is important for achieving a straight and smooth edge.
Variations in speed and pressure can lead to an uneven cut and may also put additional strain on the cutting wheel and the tool.
Proper execution of these techniques not only ensures a higher quality of work, it also helps to extend the life of your cutting wheels and tools.
Overcoming Common Challenges
Wheel Wear and Breakage
Problem: Excessive or uneven wear, and in some cases, breakage of the wheel.
Solution:
- Use the correct wheel type and size for the metal and task at hand.
- Apply consistent, appropriate pressure and maintain an optimal speed.
- Regularly inspect wheels for signs of damage or wear and replace them as needed.
Inefficient Cutting
Problem: Slow cutting speed or difficulty in making a clean cut.
Solution:
- Ensure that the wheel's specifications match the metal's type and thickness.
- Maintain the cutting tool properly and make sure that it operates at the correct RPM.
- Sharpen or replace blades regularly to keep them in optimal condition.
Heat Build-Up
Problem: Overheating of the metal or the wheel during cutting.
Solution:
- Avoid prolonged pressure in a single spot. Move the wheel steadily.
- Use a wheel with a higher heat tolerance if cutting thicker or harder metals.
- Allow for cooling periods during extended cutting tasks to prevent overheating.
Inconsistent Cuts
Problem: Jagged or uneven cuts.
Solution:
- Check the wheel’s alignment and make sure that it’s securely fitted to the cutting tool.
- Practice consistent cutting techniques while maintaining a steady speed and pressure.
- Use a guide or clamp to ensure straight cuts, especially for long or precise cuts.
Safety Concerns
Problem: Accidents or injuries due to improper use or wheel failure.
Solution:
- Always wear appropriate safety gear, including goggles, gloves, and ear protection.
- Make sure that the workpiece is securely clamped or held in place.
- Follow the manufacturer’s guidelines for wheel use and replacement.
Regular maintenance, proper technique, and using the right wheel for the job are key factors in overcoming these types of obstacles.
Ace Your Next Project with the Right Accessories from Fastener Systems
For your upcoming projects, consider Fastener Systems Inc. (FSI) as your first choice for high-quality accessories. Our extensive catalog offers a diverse range of reliable tools and fasteners, tailored to meet the demands of both professionals and DIY enthusiasts.
Contact us today to discover all of our fastener and construction project solutions!